Redan för 28 år sedan fick Cementa en innovation i sin hand som kunde kapa industrins koldioxidutsläpp. Trots det är cementtillverkning fortfarande en av världens mest förorenande industrier. Varför pratar ingen om att det finns bättre alternativ? Realtid publicerar en text av Maja Persson illustrerad av Fredrik Tjernström
Innovationen som cementindustrin mörkade

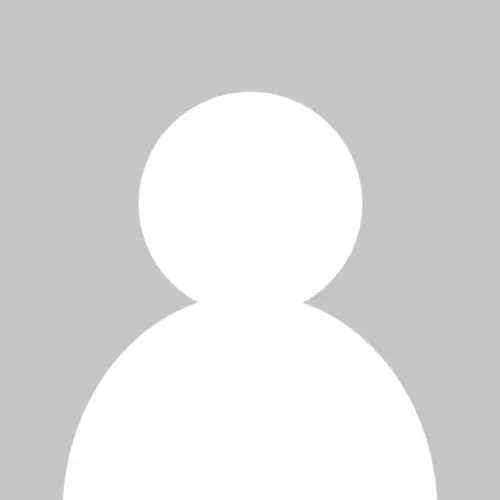
Mest läst i kategorin
Den 10 augusti 2021 ställer sig näringsminister Ibrahim Baylan och klimatminister Per Bohlund vid varsitt podium på Regeringskansliet i Stockholm. Nationella medier har bjudits in till en digital pressträff, och stämningen är gravallvarlig. Anledningen: Sverige tycks stå inför en cementkris.
Mark- och miljööverdomstolen har beslutat att företaget Cementa, som hittills har försett Sverige med 75 procent av vår cement, inte längre får bryta den kalksten på Gotland som behövs för produktionen. Branschföreträdare och fackförbund har varnat för ett svenskt byggstopp och hundratusentals förlorade industriarbeten. Under några sommarveckor har vi blivit medvetna om den enorma roll som cement – ett material som vi vanligtvis tar för givet – spelar för den mänskliga civilisationen.
Cement är nyckelingrediensen i betong, som är världens näst mest använda material efter vatten. Från Colosseum i Rom till dagens rekordhöga skyskrapor, från vägar och broar till dammar och vattenledningssystem – utan betong hade vår byggda värld inte varit möjlig.
Cementen är det grå pulver som, när det reagerar med vatten, binder ihop betongens sand och grus till en helhet med oöverträffad styrka. För att göra traditionell cement – så kallad Portlandcement – behöver man kalksten och lera, som krossas och hettas upp till 1 450 grader i massiva, snurrande kalk-ugnar. Den grundläggande processen har i princip varit oförändrad i över 100 år. Varför ändra på något så mirakulöst som flytande sten?
Men så kom klimatkrisen. Och som så ofta visar sig en av människans mest genialiska uppfinningar också vara en av de mest destruktiva.
Vid upphettningen av kalkstenen frigörs enorma mängder koldioxid, vilket gör att cementproduktionen i dag står för cirka 8 procent av världens koldioxidutsläpp. Årligen släpper cementindustrierna ut över 3 miljarder ton växthusgaser, vilket är mer än tredubbelt så mycket som flygbränslet. Om cementindustrin skulle vara ett land skulle det vara den tredje värsta koldioxidutsläpparen i världen, efter Kina och usa.
Världen står inför dubbla utmaningar: att bygga infrastruktur och bostäder åt en växande medelklass, och hindra växthusgasernas katastrofala följder.
När Bill Gates i februari höll en presskonferens angående sin bok Så undviker vi klimatkatastrofen fokuserade han på cement som en av de viktigaste klimatfrågorna att lösa. I boken skriver han att cementframställningens utsläpp inte går att komma runt: ”Det är en kemisk reaktion – kalksten plus hetta är lika med kalciumoxid plus koldioxid.”
Cementa, som med sin fabrik på Gotland står för cirka 3 procent av Sveriges årliga koldioxidutsläpp, har presenterat en långsiktig lösning på problemet. Genom att fånga in och lagra de 1,8 miljoner ton koldioxid som årligen frigörs när kalkstenen hettas upp ska man om nio år bli först i världen med koldioxidneutral cement. Den infångade koldioxiden ska kylas ned till vätskeform och skeppas i väg på fartyg till Nordsjön, för att slutligen pumpas ned i berggrunden.
Regeringen har ställt sig bakom Cementas plan och är beredd att stödja den med skattepengar – kostnader som tros uppgå till flera miljarder kronor. Detta trots att det har varnats för liknande lösningar. I en rapport från det australiska klimatrådet, i den arbetsgrupp som har bidragit till en FN-rapport om klimatet, varnar man för ”fjärran, vaga ’nettonoll-mål’”, och ”att förlita sig på att avskilja koldioxid från atmosfären”.
På pressträffen i augusti meddelar Ibrahim Baylan och Per Bohlund att man kommer att förändra miljöbalken för att tillfälligt förlänga Cementas tillstånd att bryta kalk på Gotland – en akut lösning för att undvika den kris som industrin har varnat för.
– Situationen har helt uppenbart blottat en allvarlig sårbarhet, säger Ibrahim Baylan.
Vad varken Baylan, Bohlund eller Gates verkar veta är att Sverige och världen redan för 28 år sedan hade en chans att – med en svensk innovation – undvika cementindustrins koldioxidutsläpp till att börja med.
1991 utvecklades en teknologi vid Luleå tekniska universitet, med potentialen att ersätta upp till 70 procent av den vanliga kalkstenscementen. Men mannen bakom innovationen skulle möta en mäktig motståndare: En av världens största, och mest förorenande, industrier.
I november 1991 kom Vladimir Ronin och hans familj till Luleå. Han var docent i cement- och betongteknologi, och efter nästan 20 år som avdelningschef på Research Institute of Construction Materials i Sovjetunionen skulle han gästforska vid Luleå tekniska universitet.
– Jag hade ansvarat för ett team med 20–30 personer som alla var involverade i tillämpad forskning för att stödja den sovjetiska industrin. Så ur ett vetenskapligt och industriellt perspektiv hade jag kanske en bredare erfarenhet än många västerländska forskare, som ofta har ett smalare fokus, berättar Vladimir Ronin.
Luleå tekniska universitet hade etablerats 1971 som ett vetenskapligt flaggskepp i norra Sverige, dit många unga, ambitiösa forskare kom både från övriga Sverige och världen.
– Det var en otrolig nivå på utrustningen, särskilt jämfört med Sovjetunionen som jag kom ifrån. Jag var väldigt lycklig över att få undersöka sådant som intresserade mig utan att ha något administrativt ansvar, minns Vladimir Ronin.
I 1990-talets Sverige var vi fortfarande lyckligt ovetande om cementens påverkan på klimatet, och byggindustrins fokus låg helt på att göra betongen så högpresterande som möjligt. Lennart Elfgren, som var professor i byggkonstruktion vid den institution där Vladimir Ronin gästforskade, beskriver en hög nationell uppslutning kring att göra betongen starkare:
– Det fanns ett nationellt centrum för högpresterande betong som drogs i gång av ett antal företag i branschen, bland andra Cementa, Skanska och NCC. Vi hade nationella kontakter och seminarier, berättar han.
Vladimir Ronin experimenterade med universitetets högteknologiska utrustning, däribland ett slags vibrerande kvarnar som kommer åt varenda liten partikel av det material du tillför.
– När jag körde Portlandcementen genom kvarnarna, tillsammans med andra vanliga betongtillsatser, började jag se enastående resultat. På en dag kunde jag få en betongstyrka som vanligtvis tar 28 dagar att utveckla. Jag var 40 år gammal, med 18 års forskningserfarenhet och jag tror inte på mirakel. Min första reaktion var att det här var för bra för att vara sant.
Men efter flera rengöringar av systemet och ett hundratal upprepade experiment, stod det klart för Ronin och hans kollegor att upptäckten hade ett enormt värde.
– För det första är det ett ganska enkelt upplägg, berättar han. Man behöver inte konstruera nya maskiner, utan bara använda eller modifiera maskineri som redan används i andra processer. Teknologin kräver bara en tiondel av den energi som går åt vid vanlig cementframställning, och den frigör ingen koldioxid. Jag började titta på prestandan hos materialet och fann att den var något i hästväg.
Den nya teknologin döptes till EMC, vilket står för Energetically Modified Cement. Med energimodifiering menas att det material som tillförs de vibrerande kvarnarna aktiveras. Det möjliggör en lika hög styrkeutveckling hos betongen som med Portlandcement, men med mycket längre beständighet och utan koldioxidutsläpp eller andra föroreningar.
Professorn Lennart Elfgren, som tillsammans med Vladimir Ronin skrev flera vetenskapliga artiklar om innovationen, såg också en stor potential:
– Det var ju ett sätt att göra betongkonstruktioner effektivare, säger han. Med mindre andel cement kunde man få liknande egenskaper.
Vladimir Ronin fick pengar av en lokal fabrik för vinterbetong för att testa materialet, som visade sig härdas till och med i Norrbottens lågtemperaturzon.
– Med min kunskap om byggindustrin förstod jag att det här skulle ha enorma kommersiella fördelar. Supercement, säger Vladimir Ronin.
Han ansökte genast om patent på sin upptäckt, och startade ett företag. Med pengar från Luleå kommun byggde man upp en pilotenhet som kunde producera ett ton i timmen av det nya materialet. Lokala entreprenörer byggde flera objekt med supercementen, bland annat en dricksvattendamm och en bassäng.
– Ur samhällelig synpunkt fanns det mycket att vinna på den här nya teknologin. Men cementtillverkarna var ju inte lika förtjusta, för Vladimir kunde antingen göra mycket starkare betong med samma mängd cement som förut, eller så kunde han göra lika stark betong med mindre cement, säger Lennart Elfgren.

Betong är världen näst mest använda material efter vatten, och cementindustrierna släpper ut tredubbelt så mycket koldioxid i atmosfären som flygbränslet.
Våren 1994 sändes ett inslag i svt:s Aktuellt om supercementen som hade uppfunnits i Luleå.
– Plötsligt var man en kändis på universitetet, säger Vladimir Ronin och skrattar. Intresset exploderade och jag fick genast ett samtal från Cementa, som sa att de ville testa materialet.
Enligt Vladimir Ronins utsago betalade Cementa för resan till Slite, där de hade ett eget laboratorium och forskningscenter.
– Vi körde tester som visade att vårt material hade nästan dubbelt så hög tryckhållfasthet som det Cementa kunde producera, säger han. Det var chockerande för dem.
Vladimir Ronin började få samtal från Cementas dåvarande vice vd, Fredrik Winberg.
– Han erbjöd mig att bli adjungerad professor med koppling till Cementa, och att de kunde betala mig en, i mina ögon, liten summa pengar för att skriva över innovationen på dem.
Att betala forskare lön för att knyta forskningen till industrins intressen är inte ovanligt, varken nationellt eller internationellt.
– Det är ett stort problem att forskare springer cementindustrins ärenden och blir partiska, menar Vladimir Ronin.
Cementas dåvarande vice vd, Fredrik Winberg, jobbar i dag inte i cementindustrin. Han säger att han minns Vladimir Ronin och hans innovation som en i mängden av nya idéer Cementa ville undersöka.
– Det är länge sedan nu, så jag minns inte alla detaljer. Men när man inom koncernen får reda på nya idéer gör man naturligtvis en bedömning av huruvida det här är kommersiellt gångbart eller inte. Jag kommer ihåg att vi försökte få reda på vad det här var för något, och vi fick inte direkt klarhet i det. Det var inte full transparens i det hela. Och jag minns att vi hade en diskussion med Ronin om att jobba tillsammans, vilket han tackade nej till.
Vladimir Ronin beskriver det som att Cementa kom med ett skambud.
– Att skriva över min innovation på en så liten aktör jämfört med stora internationella cementproducenter som Lafarge och Holcim, som jag också fick samtal ifrån … det kunde jag inte göra. Min känsla var att de ville köpa mitt patent för att lägga det på hyllan och låta det falla i glömska.
Lennart Elfgren, den dåvarande professorn i Luleå, minns att det redan på ett tidigt stadium var svårt att få med cementtillverkarna på tåget.
– För att göra det här i stor skala måste det helst vara någon cementtillverkare som kopplade på och integrerade processen i sin cementframställning. emc hade några eu-projekt på gång, men cementtillverkarna såg inte det här som någon stor möjlighet – snarare som en konkurrent, säger han.
Vladimir Ronin ser det som naturligt utifrån cementtillverkarnas perspektiv.
– En cementfabrik som producerar 1 miljon ton kostar ungefär 200–300 miljoner dollar. Så kan du föreställa dig ekonomin hos de företag som har kapacitet att producera 50 eller 100 miljoner ton om året? Och plötsligt kommer någon från ett litet företag i Norrbottens ödebygd, med en unik lösning som skulle halvera behovet av Cementas produkt. En teknologi som dessutom kräver en tiondel av energikonsumtionen, en fjärdedel av kapitalkostnaden, har noll utsläpp och överlägsen teknisk prestanda. Det blir ett existentiellt hot för Portlandcementbolagen.
Fredrik Winberg minns det inte som att man såg Ronins uppfinning som ett hot mot Cementas kärnverksamhet.
– Men ett företag måste ju göra bedömningen utifrån vad som är bra för företaget. Man har ju ett ansvar gentemot ägarna. Nu för tiden jobbar jag själv med en ny innovation – avancerade kompositer – och då vänder jag mig ju inte till de företag som jag tror att det kan vara en nackdel för.
Vladimir Ronin insåg snart att hans innovation skulle möta mäktigt motstånd.
– Lennart Elfgren började säga att jag behövde en advokat, och han hade rätt. När jag tackade nej till att samarbeta började Cementa blockera varenda möjlighet, och mitt företag hamnade i en fruktansvärd situation.
Ett par år senare kom Vladimir Ronin genom gemensamma bekanta i kontakt med den norske entreprenören och investeraren Atle Lygren, som tidigare hade byggt upp flera framgångsrika sjöfartsbolag. En snöig eftermiddag i Luleå berättade Vladimir Ronin för Atle Lygren om teknologin som kunde minska mängden Portlandcement i betong med nästan 50 procent.
– Jag lyssnade och lyssnade, och efter en stund fick jag gåshud på armarna, minns Atle Lygren. Jag insåg att om det han berättade var sant skulle jag kunna vara med om att transformera en av världens största industrier, bidra till en enorm minskning av dess koldioxidutsläpp och andra föroreningar, och samtidigt tjäna mycket pengar. Jag förstod också att hans företag hade slut på pengar. Jag visste ingenting om ekonomin kring cement då, men jag blev väldigt rädd att få läsa i tidningen att någon annan hade tagit chansen att stödja honom.
Två månader efter att Atle Lygren kom tillbaka till sitt hem i Verbier investerade han 20 miljoner kronor i Ronins teknologi.
– Genom åren har jag investerat minst tio gånger så mycket. I dag har vi en industriellt bevisad teknologi som kan minska cementindustrins koldioxidutsläpp med minst 70 procent – en global potential på 3 miljarder ton om året.
Senare samma år, 1996, vann innovationen Médaille d’Or avec Mention på den 45:e World Exhibition of Invention, Research and Industrial Innovation.
Vid det här laget hade en patentstrid satt i gång, som skulle vara i nio år. Några månader efter att Ronin fått patent på sin innovation ansökte Cementa om patent på en snarlik teknologi. Cementas patentansökan avslogs, varpå Cementa försökte bestrida Ronins patent genom att hävda att teknologin redan var känd.
– Svenska patentverket avvisade Cementas invändningar, och då gick de vidare till det europeiska patentverket i München, berättar Vladimir Ronin. Den här processen, där Cementa opponerade sig mot våra patent, gick så långt att vi fick ett slutgiltigt beslut i den europeiska patenträtten först 2002, då vi återigen fick rätt. Från 1993 till 2002!
Cementas dåvarande vice vd Fredrik Winberg påpekar att det inte är ovanligt att bestrida patent inom den industri där man verkar.
– Det var nog inte den enda gången vi hade invändningar mot patent, säger han. Traditionellt gör man så när det kommer en patentansökan. Man tittar på det och om man inte tycker att det är nytt så påpekar man det.
Utvecklingen från liten till stor skala försvårades enligt professorn Lennart Elfgren också av de dåvarande europeiska normerna för godkänd cement, som var satta utifrån cementjättarnas verksamhet.
– De var gjorda så att de beskrev hur cementen skulle vara komponerad – vilka innehåll den skulle ha och hur mycket det skulle vara av de olika ingredienserna. Det var den europeiska cementindustrin som låg bakom det där. Man gick inte på funktionen utan beskrev innehåll och framställningsteknik. Och den här nya, energimodifierade cementen passade inte in i den normen, eftersom man med den kunde få liknande betongegenskaper på ett helt nytt sätt, förklarar Lennart Elfgren.
I stället för att kämpa för att få stöd i Sverige och Europa sökte sig Atle Lygren och Vladimir Ronin till USA, där cementnormerna var fokuserade mer på betongens slutliga funktion och resultat än på ingredienser och framställningsteknik.
Vid det här laget började världen också sakta få upp ögonen för problemet med cementugnarnas koldioxidutsläpp.
– På 1990-talet hade det här med växthusgaser aldrig varit någon faktor, säger Vladimir Ronin. Då handlade allt om att göra betongen så högpresterande som möjligt. Om det också var bra för miljön var det bara en bonus.
Men bonusen, att Ronins uppfinning också betydde kraftigt reducerade koldioxidutsläpp, skulle bli än mer relevant.
Eftersom EMC-teknologin innebär att materialet inte behöver hettas upp utan blir reaktivt med hjälp av de vibrerande kvarnarna, kan man undvika de koldioxidutsläpp som oundvikligen sker vid traditionell cementframställning. Om 70 procent av Portlandcementen kan ersättas med det energimodifierade materialet skulle de nuvarande koldioxidutsläppen från cementindustrin alltså kunna minska med 70 procent.
År 2000 blev Ronins och Lygrens gemensamma företag, EMC, inbjudna till en konferens i Washington DC om ”Low Carbon Cement”, som hölls av American Society of Civil Engineers.
– Det var troligen en av de första nationella konferenserna om ämnet, säger Vladimir Ronin, som då var adjungerad professor vid Luleå tekniska universitet.
Genom konferensen fick de kontakt med ett stort företag som drev kolkraftverk, med högkvarter i Houston i Texas, av vilka de skulle kunna köpa flygaska. Så småningom fick de också kontakt med Texas Department of Transportation, US Federal Highway Administration och ett familjeägt företag i Texas som producerade färdiggjord betong.
2004 kunde en fabrik för energimodifierad flygaska dra i gång i full industriell skala. Texas Department of Transportation blev kunder, liksom US Federal Highway Administration ett år senare. Den energimodifierade flygaskan användes nu i bred skala, i allt från allmän infrastruktur som motorvägar, broar och hamnar till kommersiella byggen och bostäder. Det spanska byggföretaget Ferrovial och det irländska byggmaterialföretaget CRH blev också kunder.
Inom två år blev företaget lönsamt. Under sju år producerades flera miljoner kubikmeter betong med 50–60 procent av EMC:s energimodifierade flygaska.
Hittills hade Ronins och Lygrens företag EMC använt sig av flygaska från kolkraftverk till sitt energimodifierade ersättningsmaterial. Men i och med den industrins miljöomställningar insåg de att sådana restprodukter snart inte skulle vara en långsiktig råvarukälla. De började undersöka möjligheten att använda naturliga puzzolaner – vulkaniskt material som finns där vulkanisk aktivitet någon gång ägt rum.
Att använda vulkaniskt material till att göra betong är knappast något nytt. I Romarrikets betongkonstruktioner användes cement med vulkanisk aska, som kallas just puzzolaner efter halvön Pozzuli där romarna utvann den. Den antika betongen, som romarna kallade concretum, användes till byggnader, akvedukter, amfiteatrar, dammar och hamnar. Mycket av detta, exempelvis Pantheon, står kvar än i dag.
Den flygaska som Vladimir Ronin och Atle Lygren hade använt dittills kom från kolkraftverk. De visste att vulkanaskans kemiska sammansättning är väldigt lik flygaskans, och att den ingick i materialstandarderna för betong och cement i både usa och Europa.
– Vi insåg att längs västkusten i USA och delar av Kanada, nästan hela vägen från West Texas till Alaska, finns det i princip obegränsade mängder vulkaniskt material, säger Atle Lygren. Så vi startade en pilotfabrik i Kalifornien för forskning och utveckling och körde tester på olika naturliga puzzolaner. Vi ville vara helt säkra på att uppnå samma resultat som med flygaskan. 2014 fick vi patent på vulkanaskaprocessen.
En investeringsfond i Kalifornien erbjöd sig att investera 50 miljoner dollar i EMC:s Kalifornienbolag, för att bygga två fabriker i norra och södra Kalifornien där man kunde aktivera vulkanaska med hjälp av EMC-teknologin.
– Killarna hävdade att Abu Dhabis kungahus skulle bli en av investerarna, och att de hade kontakter på hög politisk nivå, minns Vladimir Ronin. Vi förhandlade om ett avtal där varje part skulle äga cirka 50 procent av vårt Kalifornienbolag. Men allt eftersom due diligence-processen framskred och bekräftade vår teknologi blev de så besatta av projektet att de började kräva rätten att investera i hela Nordamerika och halva världen. Till slut tappade vi tilliten till dem och vi var tvungna att avsluta förhandlingarna.
Det blev ingen investering, och vad som därefter hände beskriver Vladmir Ronin och Atle Lygren som skandalöst.
– Killarna med investeringsfonden gick bakom våra ryggar till våra ”vänner” i Texas. De kom överens om att försätta vårt Texasföretag i likvidation för att sedan köpa innehållet i fabriken och betala av killarna i Texas. De hoppades på att få tillgång till våra företagshemligheter och bilda ett eget bolag, baserat på vår teknologi.
Lygren och Ronin tog det hela till District Court i Texas, där de vann med en större summa pengar i skadestånd.
– Juryn kramade om oss och sa att de skämdes över att något så korrupt kunde hända i Texas, minns Vladimir Ronin.
Motståndarna överklagade till Texas Court of Appeal, där de också förlorade, och sedan ända upp till Supreme Court.
– Supreme Court ville först inte ens titta på det, säger Vladimir Ronin. Men killarna med investeringsfonden lyckades övertyga domstolen att revidera sitt beslut, med konsekvensen att vi berövades både skadeståndet och fabriken. Förra året, när jag fick den slutgiltiga domen, fick jag nästan en hjärtattack.
Vad hände sedan – de kan väl inte använda en teknologi som ni har patent på?
– De trodde att de skulle kunna ersätta våra vibrerande kulkvarnar med ett annat system och få liknande resultat till en konkurrenskraftig kostnad. Vi har inte alla detaljer, fabriken är fortfarande i gång men dess tekniska och ekonomiska potential är begränsad trots att de inskränker på våra patent, säger Lygren.
Under den tid då EMC verkade i USA hade spelplanen börjat förändras radikalt i Europa. Klimatkrisen har nu satt cementindustrin i rampljuset, och pressen är hög på att hitta alternativ till traditionell cement och betong.
Svante Axelsson, som är miljöekonom och nationell samordnare för Fossilfritt Sverige, tror att det nu finns en ökad marknad för lösningar som EMC.
– Den klimatneutrala cement som Cementa vill producera med hjälp av koldioxidavskiljning kommer ju att bli 70 till 100 procent dyrare, säger han. Och det är då alternativen får sin chans. Byggindustrin har redan börjat effektivisera för att det blir så dyrt, och det kommer att bli ännu dyrare.
Vad krävs för att stora företag, som omsätter enormt mycket pengar, ska ställa om hela eller delar av sin verksamhet och kanske bli mindre lönsamma?
– Det handlar mycket om konkurrens, säger Svante Axelsson. Statens uppgift måste vara att hålla konkurrensen levande och inte få oligopol- och monopolsituationer, som har en konserverande effekt på marknaden. Det är intressant att utan Elon Musk hade vi inte haft den här snabba förändringen av bilindustrin. De ville inte byta system egentligen, de ville hålla på ett tag till med förbränningsmotorer. Men när de märkte att Elon Musk kunde sälja så mycket och det blev en attraktion kring elbilen var de helt enkelt tvungna att ställa om.
Hur gör man för att släppa in nya innovationer i en gammal industri?
– Vi har skapat en seminarieserie där vi har bjudit in startups och frågat oss om det är så att det gamla dödar det nya. Som i en gammal skog, där det nya plantorna inte får tillräckligt med ljus. Innovation har ju varit en svensk framgångsresa sedan lång tid tillbaka, så vi får inte stelna till utan måste ha dynamik i näringslivet. Vi är ganska bra på att stötta innovationer fram till demostadiet, men för att gå från det till storskalig verksamhet krävs framför allt risktagare. Det finns enormt mycket pengar i systemet nu när man letar efter hållbara lösningar. Men de flesta vill gärna glida in efter att någon annan har tagit risken. I den här transformativa tiden behöver staten därför utveckla sin roll.
Ronny Andersson, chef för forskning och innovation på Cementa i Sverige som har jobbat inom företaget i över 30 år, tycker att det är en spännande tid.
– Utåt är det väldigt mycket fokus på cementindustrins koldioxidavskiljning för att kunna bli helt klimatneutrala. Men internt jobbar vi också febrilt med lösningar för succesiva förbättringar som kanske kan implementeras inom fem år. Där är det ett oerhört fokus på olika naturliga råvaror som värmebehandlade (kalcinerade) leror, och vulkanaskor som redan är naturligt värmebehandlade. Med rätt kemisk sammansättning är de möjliga att använda. Och det är det som emc, om jag har förstått det rätt, jobbar med. Det kommer säkert att kunna användas i väldigt många länder som har stora mängder sådana material.
Andersson påpekar att kunskapen om naturliga material har funnits länge.
– Jag har själv till exempel jobbat med vulkanisk aska när det var populärt som alternativ till lättklinker, och då får man se fördelarna med de här materialen. Men på något sätt har det tidigare inte funnits riktiga drivkrafter för dess användning.
Ronny Andersson nämner två faktorer som han menar har förändrat förutsättningarna för nya alternativ i betongbyggandet. Den ena handlar om att standarderna för betong har ändrats.
– Vi har precis fått igenom en standard som möjliggör en ökad användning av tillsatsmaterial. Från materialspecifikationer vill man i stället gå över till betongens funktioner. Och det är ju en direkt och konkret möjlighet att göra relativt stora minskningar i klimatpåverkan, utan att påverka betongens livslängd eller funktion.
Den andra faktorn har att göra med eu:s utsläppssystem för industrier. De innebär att om cementindustrin överträder en utsläppsgräns måste man köpa utsläppsrätter på en öppen marknad.
– EU har sedan 2005 skruvat åt det mer och mer för varje år, så varje år måste vi minska klinkertillverkningens koldioxidutsläpp mer, men med samma produktionsmängd. Det har stor påverkan på vår verksamhet.
Kanske har tiden slutligen blivit mogen för Vladimir Ronins innovation.
– Vladimir och jag har jobbat oss igenom de här 25 åren. Trots alla hinder som cementindustrin har satt upp gentemot revolutionerande innovationer som vår – exempelvis genom att försöka kontrollera betongstandarderna – har vi äntligen nått en punkt i historien då vi har en industriellt bevisad teknologi, och en produkt som kan stå för 70 procents minskning av cementindustrins utsläpp. Vi är inblandade i ett antal processer för att finansiera en storskalig implementering av den här teknologin. Förhoppningsvis blir vi nu belönade för alla de här årens uppoffringar, som vi mestadels har gjort helt på egen hand, säger Atle Lygren.
I augusti förlängdes Cementas kalkbrytningstillstånd på Gotland i åtta månader. Någon vecka senare meddelade Högsta domstolen att man inte ger Cementa prövningstillstånd, och de kan tvingas stänga ned om de inte får ett nytt tillstånd inom knappt ett år. Till Svenska Dagbladet meddelar hållbarhetschefen Karin Comstedt Webb Cementas plan B: att under en övergångsperiod köpa in kalken från externa leverantörer.
Men varningarna för en cementkris och nationellt byggstopp väcker frågan om varför Cementa inte skulle kunna importera och distribuera cementklinkern i stället för att köpa eller bryta mer kalk. Tyska Heidelberg Cement, som äger Cementa, har över 50 fabriker bara i Europa och Nordafrika och dessutom en global cementhandelsverksamhet – skulle inte de kunna förse Sverige med de 2 miljoner ton cement som fabriken i Slite tidigare har producerat?
Karin Comstedt Webb, hållbarhetschef på Cementa, ger följande bild:
– Det handlar främst om tre saker, säger hon. För det första är det just nu ett oerhört hårt tryck på byggvaror i hela Europa, så det finns ingen överkapacitet någonstans. Så varken ur ett kort eller långt perspektiv går det att förlita sig på import. Sedan är det väldigt stora volymer av ett tungt material vilket kräver logistik i form av hamnkapacitet, terminaler och omlastning. Vår bedömning är att det skulle ta åtminstone tre till fyra år att få import på plats, och då exponeras svensk försörjning för helt andra osäkerheter knutet till leveranstrygghet. Den tredje faktorn är att alla cement- och betongrecept i Sverige bygger på den svenska cementen som har utvecklats och anpassats under många år. Så det är möjligt att man skulle kunna få fram en importlösning, men då är det några år framåt i tiden. Den skulle sammantaget leda till större risker knutet till svensk försörjning och beredskap, och vi skulle ge oss själva en väsentligt sämre utgångspunkt för att klara klimatmålen.
Comstedt Webb pekar på samma sårbarhet som Ibrahim Baylan menar nu har blottats. Flera byggföretag rapporterar att de vill bli mindre beroende av en enda aktör för cementförsörjningen.
Atle Lygren säger att en nedstängning av Cementas fabrik innebär ett gyllene tillfälle för Sverige att leda utvecklingen mot att minska industrins koldioxidutsläpp. Med sin erfarenhet av sjöfartstransport ser han det inte som komplicerat att i ett första led importera cementklinkern i stället för att bryta kalk.
– Enligt mina undersökningar finns det en anmärkningsvärd överkapacitet vad gäller cementproduktion i Europa, liksom i Turkiet, Nordafrika och så vidare. Importerad cementklinker skulle använda samma distributionsnätverk som det som nu används för Slite-produktionen. Och mig veterligen är den cement som produceras i Slite inget speciellt jämfört med cement från en rad andra källor, vilken man dessutom skulle kunna göra enkla modifieringar av.
Han hänvisar till en fabrik i Nederländerna, som också ägs av Heidelberg Cement och som nyligen genomgick en liknande omställning. Fabriken har en liknande cementkapacitet som Cementas, och stängde 2019 sin klinkerproduktion för att i stället importera klinker, mala den till cement och distribuera i landet. Enligt Globalcement.com blev endast 50 personer av med sina jobb.
– Nederländerna konsumerar minst dubbelt så mycket cement som Sverige. Om de kan leva på cementimport kan Sverige det också, och om Heidelberg kunde lösa det där kan de lösa det även i Sverige. Skulle de inte kunna det så kan vi erbjuda en lösning: Stäng kalkbrytningen och klinkerproduktionen, och som en kortsiktig lösning importera klinkern till Slite för att mala ned den till cement. Kalkbrottet och den koldioxidutsläppande delen av fabriken kan då stängas, och vi kan använda det mesta av den resterande utrustningen till att mala både den importerade klinkern till cement (45 procent) och vulkanaska (55 procent). Vulkanaskan kan sedan aktiveras med de utsläppsfria vibrerande kulkvarnarna, för att blandas med den malda cementklinkern till certifierad cement som slutligen kan säljas till hela Sverige – via samma värdekedja och distributionskanaler som Cementa använder i dag. Så fort betong- och cementstandarderna tillåter det kan vi ersätta 70 procent av cementen med vårt material, och då behöver vi bara 30 procent cementklinker. Enligt våra beräkningar skulle inte en sådan omställning kosta det svenska folket mer än vad cementproduktionen gör i dag.
En sådan lösning skulle bli fördelaktig för era affärsintressen.
– Självklart. Men man behöver göra en mycket bredare definition av vad man menar med intressenter. Den första och främsta intressenten är Moder Jord och allt liv här. Nummer två är de människor som faktiskt kan göra skillnad. Redan för 28 år sedan hade Sverige den här möjligheten i sin hand, att med en svensk uppfinning driva utvecklingen mot noll koldioxidutsläpp från cementproduktionen. Hade man fångat den möjligheten då hade vi varit färdiga med det nu, eller åtminstone på väldigt god väg. Vi hoppas att Sverige fångar möjligheten den här gången.
Maja Persson är journalist. Favoritkonstruktioner i betong är Pantheon och ett tårtfat som hennes mamma har gjort.
Fredrik Tjernström är illustratör. Han hoppas att tiden nu är inne för EMC:s cement att användas i stor skala.